Performing roofing maintenance regularly helps homeowners find and fix issues before they become major problems. This saves homeowners money and stress down the road, especially in the event of a severe storm.
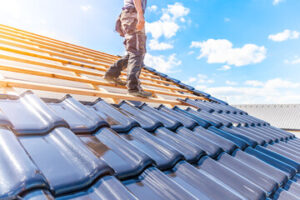
Homeowners should also check trees around their home for signs of health issues like dead limbs that could easily snap during high winds. This includes noticing discolored leaves, cracks in the bark, and withered branches. Visit https://www.jmelitecontractors.com to learn more.
Whether a roof has sustained damage from heavy storms or is aging, regular visual inspections can identify problems early and prevent them from becoming more significant. These inspections help businesses save money on costly repairs and maintenance, while also preventing water damage to interior structures.
A typical roofing inspection includes an initial conversation about the condition of the facility’s roof and any current or previous damage that may have occurred. It is a good idea to have these conversations just after a major storm has passed, so the roofer can check for any damage that may have been caused by the heavy rains.
The next step is to physically inspect the roof structure and equipment. The roofer will start with the perimeter and work their way toward the center of the building. This is because the outer areas tend to experience more wear and tear, so it is important to catch any potential issues with their early stages. In addition, the roofer will check gutters, base flashings, and counter flashings. They will also look for a drain clog or an expansion joint that may be cracking or breaking.
When the inspector has walked the entire perimeter of the roof, they will check for any obvious signs of damage or wear on the surface. This can include sagging areas, missing shingles, or debris accumulation. The roofer will also take a close look at any penetrations on the roof, such as vents, skylights, and HVAC units. This is because they are often a source of leaks. The roofer will also check the roof’s flashing and seals, as well as its expansion joints.
Depending on the type of roof, the inspector might also inspect the attic or crawlspace. This is to check for any leaks or mold, which could indicate that the insulation needs replacement. Infrared scanning is an advanced inspection technique that can identify moisture trapped beneath the roof membrane. However, it should not be used to replace a visual inspection. This is because it cannot be used on inverted roofs, which have a membrane underneath the insulation and are therefore difficult to inspect visually.
Flashing Inspections
Flashing is sheet metal fabricated to a specific shape that seals vulnerable areas like roof edges, chimneys and vents. Incorrect installation of flashing can allow moisture to penetrate the roofing materials and into the home structure. A roofing contractor will inspect all the flashing on a roof and assess its condition.
The roof flashing inspection will include a close examination of the metal flashings, which deflect rain water away from roof penetrations and into the gutter system. Contractors will be looking for rust and corrosion, as well as a secure attachment to the roof deck. They will also check for gaps and cracks that may allow water to penetrate the roofing material or structural components of the home.
If a contractor finds any of these issues, they will repair and replace the damaged shingles or flashing. They will also use a caulking gun to repair any cracks and gaps in the flashings. They will note the repairs and the conditions of the flashings for future reference, and they will keep an eye out for any leaks that may develop in the near future.
Another important aspect of the roof flashing inspection is the close examination of any pipe boots and other roof penetrations. A contractor will be checking for the proper sealing of these areas, which are a common source of leaks. They will also be on the lookout for any leaks that may have developed around these areas, as well as the presence of any moss or algae growth that may indicate excess moisture.
The contractor will also examine the sidewall and head wall flashing, which protect against leaks from water moving off the roof into walls and through stucco systems. A common problem is that flashing that is too short, especially at the head wall, or that fails to extend up behind the exterior wall covering. This can lead to a weak point in the wall or stucco system. In this case, the contractor will re-flash the area and use a caulking compound that is compatible with the wall and roof coverings.
Overall Structure Inspections
When you’re doing your visual inspection, pay attention to the structure of your roof. Aside from any shingles that need repair or replacement, look for areas of deterioration that can lead to leaks. Gaps or cracks in flashing can compromise the protective seal against water intrusion, while improperly installed roof vents and skylights can also allow unwanted moisture into your building. Also look for sagging or bulging sections of the roof that may indicate the need for support structures to be added.
A structural inspection is conducted by a qualified structural engineer and offers a much more detailed assessment of the condition of your home or commercial property’s foundation, walls, framing, and roofing. During this type of inspection, the engineer will analyze each critical load-bearing component and assess whether or not it’s able to handle the current loads it’s bearing and any future loading that may occur.
The engineer will start with a thorough examination of your foundation and footers, as well as the walls, joists, beams, and columns that are supporting the roof. He or she will then move on to the living area, checking ceilings for cracks and taking pictures to document these issues. After this, the engineer will move on to other rooms and inspect these areas as well.
In addition to these essential components, the structural inspection will also include a review of any ventilation equipment present on your roof. This can include neoprene pipe boots, turbine vents, and ridge vents, which should all be properly functioning to ensure adequate roof ventilation. A structural inspection should also check the condition of any roof penetrations such as chimneys, skylights, and plumbing fixtures to make sure they are not allowing unwanted moisture into your building.
A structural inspection should also include a review of the overall condition of your roof surface, including the condition of the gutters and downspouts. The inspector will check for deterioration and make recommendations regarding any repairs that should be made. Additionally, he or she will also inspect the condition of expansion joints that allow the roof to expand and contract in response to temperature changes.
Built-Up Roofing (BUR) Repairs
Built-up roofing, or BUR, is one of the oldest and most durable commercial roof systems. Its multiple layers provide exceptional protection from the elements, including water, and are suitable for a variety of climates. It is a popular choice for large structures, and can also be topped with a reflective coating to save energy costs.
Like any other kind of roof, it is important to perform regular inspections to detect and repair damage. When a problem is noticed, it should be repaired immediately to prevent further damage and potential leaks. In addition to preventing water leaks, regularly performing maintenance on a BUR system can extend its lifespan.
BUR roofing is a multi-layered roofing system that is typically composed of reinforcing fabrics, bitumen, and asphalt. The fabric sheets (often made of fiberglass) are installed over a base sheet of insulation or the building’s original roof deck. Bitumen is then applied in a layer and heat-sealed with hot asphalt or a cold-processed adhesive to create the roof membrane. The resulting roof is then capped with a layer of aggregate, often gravel or mineral granules.
Due to their durability, BUR roofs are resistant to abrasions, unlike single-ply membranes that can be punctured with tools or even pierced by a screwdriver. They are also highly effective in protecting against water damage, and it is common for them to be coated with protective coatings, which can help prevent the deterioration of the underlying roof.
Like any other roof, a BUR system can be damaged by harsh weather conditions or improper installation. It is also important to perform biannual inspections and maintenance on a BUR system to ensure that it is functioning as intended. During these inspections, the roof should be assessed for areas of wear, and any damaged sections should be repaired immediately to avoid further damage. The longer a problem goes untreated, the more difficult it will be to repair. When repairing a BUR roof, it is critical to use a tried and true roofing contractor with experience and expertise. This is particularly important, as a poorly installed BUR system can be susceptible to water leaks and ponding water.